Fondata nel 1969 da Luigi Pozzoli a Carate Brianza (MB), Poliplast vanta una storia di oltre 50 anni durante i quali ha affrontato uno…
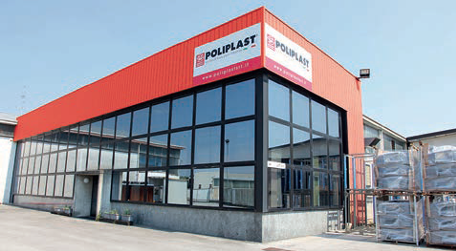
Fondata nel 1969 da Luigi Pozzoli a Carate Brianza (MB), Poliplast vanta una storia di oltre 50 anni durante i quali ha affrontato uno sviluppo ritmato da più tappe, ognuna delle quali decisiva per approdare al suo ruolo attuale di azienda protagonista sul mercato europeo.
Al centro dell’attività di Poliplast, che oggi ha la sede principale ad Albiate (MB), la produzione di paraurti per veicoli commerciali e pesanti per il settore aftermarket, prodotti di qualità equivalente all’originale per i veicoli delle Case costruttrici europee: Citroën, Daf, Fiat, Ford, Iveco, Man, Mercedes, Nissan, Opel, Peugeot, Renault, Scania, Volkswagen, Volvo.
Con un fatturato 2019 pari a 12,5 milioni di € (+10% sul 2018) e una prospettiva di crescita stimata a 13 milioni nel 2020, questa impresa tutta familiare ha saputo superare i limiti della classica PMI italiana, raggiungendo una dimensione operativa interessante e solida, che le permette di guardare al futuro con ottimismo.
Dagli esordi ai giorni nostri
Per ripercorrere i momenti più importanti della crescita di Poliplast abbiamo incontrato Umberto Pozzoli, figlio del fondatore, oggi alla guida dell’azienda nel ruolo di CEO, affiancato dal fratello Carlo, Direttore di Produzione. “Come spesso accade nella storia delle aziende italiane tutto è iniziato in un piccolo garage, dove mio padre Luigi nel 1969 iniziò a realizzare manualmente piccole parti di carrozzeria in metallo. Dopo avere lavorato alcuni anni come battilastra per un’azienda che faceva lamierati per l’Alfa Romeo, infatti, quando questa fu costretta a chiudere era riuscito a ottenere una vecchia trancia e alcuni fogli di lamiera al post della liquidazione. Tutto ha avuto inizio così: da un’apparente disavventura è nata l’avventura di Poliplast”. Negli anni, grazie all’ausilio di macchinari industriali, la produzione si fece sempre più meccanizzata e nell’86 dai paraurti in metallo si passò a quelli in poliuretano. Nel 1996 questo materiale difficile da lavorare,
molto costoso e non riciclabile, fu sostituito dal polipropilene, oggi utilizzato da tutte le Case costruttrici. Questo polimero termoplastico riciclabile è infatti caratterizzato da un elevato carico di rottura, una bassa densità, una buona resistenza termica e all’abrasione. La sua lavorazione richiede una tecnologia dedicata, macchinari dal costo elevato e personale professionalment preparato. Prosegue Pozzoli: “Un altro passaggio decisivo risale al 2000, quando all’attività di stampaggio integrammo la progettazione e la costruzione degli stessi stampi utilizzati per produrre i paraurti grazie alla tecnologia di reverse engineering”.
In sostanza, partendo dalla digitalizzazione in 3D dell’oggetto fisico si progetta e si modella lo stampo per poi realizzare il manufatto. “Avviare questa nuova attività – continua Pozzoli – ha comportato investimenti significativi in macchinari, software e personale dedicato, da formare e aggiornare periodicamente sulle nuove tecnologie adottate. In Poliplast ci impegniamo a rendere solide le competenze di chi lavora con noi: io credo che il vero valore aggiunto di un’azienda siano le persone”. Una scelta che riflette una governance aziendale allineata con i propri obiettivi e orientata alla continuità e alla coerenza con il proprio mercato.
Attività, struttura e numeri
In Poliplast lavorano attualmente 70 dipendenti: 12 negli uffici, 10 nel reparto di progettazione e costruzione stampi e i restanti distribuiti tra magazzini e produzione. L’azienda completa l’intero ciclo di realizzazione del paraurti: dalla progettazione e creazione dello stampo allo stampaggio, dai vari assemblaggi (operazioni di saldatura a ultrasuoni, incollaggi, avvitature meccaniche) alla verniciatura, fino all’imballaggio e alla spedizione.
Spiega Pozzoli: “Facciamo tutto ‘in casa’, nella sede principale di Albiate, dove ci siamo trasferiti: su un’area coperta di 5mila m2 si concentra il 70% circa della produzione e oltre alla linea di verniciatura trovano spazio 4 linee di stampaggio e l’officina stampi di 2mila m2.
Abbiamo poi un nuovo deposito di 7mila m2 che si affianca all’unità di 5mila m2 già adibita a magazzino spedizioni. A Verano (MB), invece, si trova l’altra sede produttiva: 7mila m2 con 2 linee di stampaggio e altri magazzini. L’insediamento produttivo di Poliplast raggiunge la superficie totale di 26mila m2”.
Il mercato
Specializzata nel segmento di mercato che comprende veicoli commerciali leggeri e veicoli pesanti, Poliplast ha esordito sul mercato dell’aftermarket nel 2004. Una scelta dettata da più motivi: “Dopo anni di attività nell’OE (dove manteniamo un’unica collaborazione con il Gruppo Volkswagen), è emersa l’esigenza di agire con più autonomia, sganciandoci da logiche che rischiavano di limitare la nostra voglia di fare e di crescere. Dall’avere pochi clienti, seppure di dimensioni elevate, siamo passati agli oltre 400 odierni e a una produzione annua di 500mila pezzi”. Con l’ingresso nello IAM, Poliplast ha privilegiato i mercati esteri di Europa, Nord Africa e Turchia. Un orientamento che è proseguito fino a qualche anno fa: “Da qualche anno – conferma Pozzoli – guardiamo al mercato italiano con grande interesse, anche se il nostro fatturato è costituito ancora per l’80% dall’export. Il nostro è un Paese difficile, la concorrenza è elevata e ci sono molti importatori, ma noi ci impegniamo a garantire un ottimo servizio e registriamo risultati in crescita”.
Poliplast si affida a distributori internazionali per l’estero e raggiunge distributori nazionali, regionali e ricambisti in Italia: “È una nostra ferrea regola fermarci ai ricambisti, senza rivolgerci direttamente a officine e carrozzerie”.
Sempre più decisivo, inoltre, il peso dell’ecommerce: “Abbiamo inaugurato le vendite online all’inizio del 2019 partendo da zero e oggi il 20% del nostro fatturato è generato dall’e-commerce. E la quota è in aumento costante. Sono certo che questo trend proseguirà, perché si tratta di un sistema molto veloce e comodo”.
Il futuro è adesso
I nuovi trend della mobilità – dalle motorizzazioni alternative alla guida autonoma, agli ADAS e la digitalizzazione, per citare i più dirompenti – preoccupano molti operatori del settore. La domanda, quindi, è di rito: quanto questo cambiamento impatta sull’attività di Poliplast?
“Siamo consapevoli della trasformazione in atto, ma valutando anche le analisi degli esperti pensiamo di non risentirne ancora per diversi anni. La guida autonoma non è ancora una realtà oggettiva e ci vorrà molto tempo prima che l’attuale parco circolante venga sostituito totalmente da veicoli autonomi. L’utilizzo degli ADAS, già affermato, non annulla l’incidentalità e quindi la domanda di ricambi. Anche noi, all’interno dei paraurti che produciamo, prevediamo spazi e supporti dedicati all’inserimento dei sensori montati successivamente dai carrozzieri”.
Anche questa semplice operazione, che deve garantire la perfetta corrispondenza dei fori presenti sul paraurti di Poliplast con quelli degli originali OE, viene svolta dall’azienda con l’ausilio della tecnologia più aggiornata, attraverso uno scanner e un robot antropomorfo dedicati.
Un approccio all’avanguardia
“Se nel nostro settore la tecnologia dei materiali ha raggiunto risultati ormai assodati – continua l’AD – è soprattutto nei macchinari, nei software e nel processo di reverse engineering che assistiamo a continue evoluzioni. E noi stiamo al passo: in azienda abbiamo uno scanner ottico di ultimissima generazione, che nel giro di mezzora è in grado di produrre la copia in 3D del manufatto da produrre, con una precisione centesimale”.
Non solo, l’attenzione a temi di estrema attualità come la sostenibilità ambientale e il contenimento dei costi energetici è molto viva.
“Siamo molto sensibili all’ottimizzazione dei consumi e quindi dei costi, e anche all’ecologia: le nostre linee produttive sono equipaggiate di motori elettrici a inverter, che garantiscono consumi ridotti del 20-30% rispetto ai motori elettrici tradizionali. Abbiamo investito anche nel fotovoltaico, che soddisfa il 30% dei nostri consumi energetici. Usiamo sistemi di refrigerazione free cooling, che richiedono il 30% in meno circa di energia elettrica. Due anni fa abbiamo installato un combustore termico catalitico per abbattere le emissioni in atmosfera, che oggi sono di tre volte inferiori al limite imposto da Regione Lombardia. Ci consideriamo ecologicamente all’avanguardia: quest’attenzione all’ambiente è un’eredità di mio padre, un uomo che amava molto il suo
lavoro ma anche la natura, la montagna e la vita. E noi cerchiamo di trasmettere questi valori ai nostri figli, insieme alla passione con cui facciamo questo mestiere”.
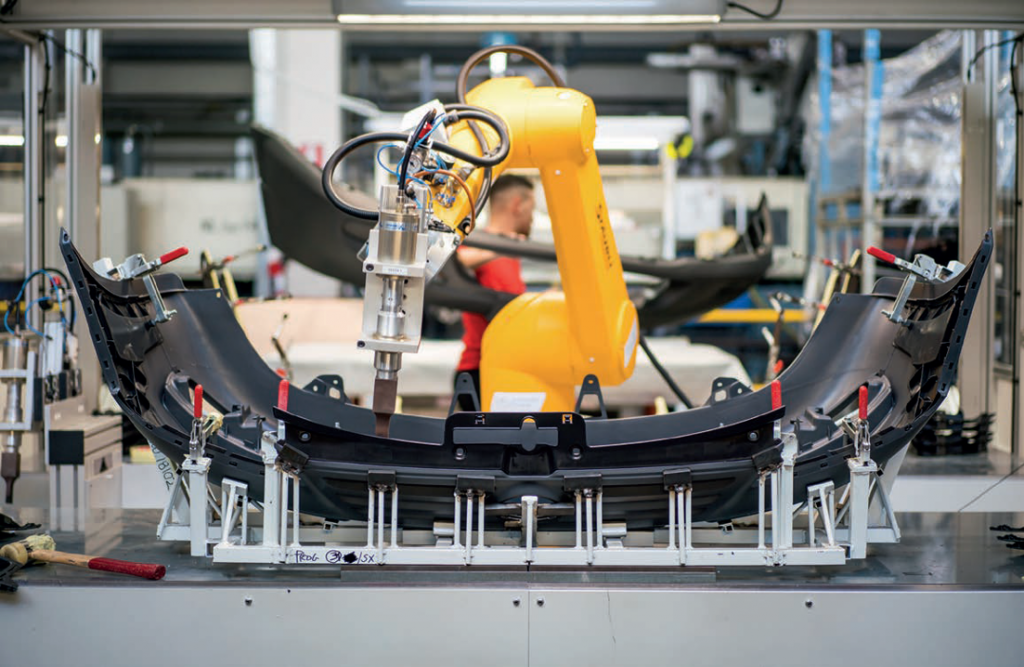
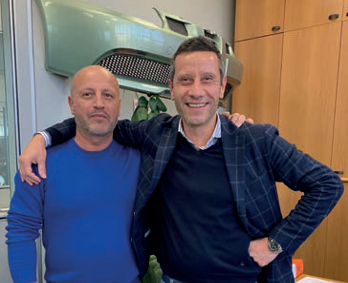
a cura di Redazione
Condividi l'articolo
Scegli su quale Social Network vuoi condividere